US Aerospace 3D Printing Market Overview
The US Aerospace 3D Printing Market Size was estimated at 336 (USD Million) in 2023. The US Aerospace 3D Printing Market Industry is expected to grow from 403.2(USD Million) in 2024 to 2,061.16 (USD Million) by 2035. The US Aerospace 3D Printing Market CAGR (growth rate) is expected to be around 15.989% during the forecast period (2025 - 2035).
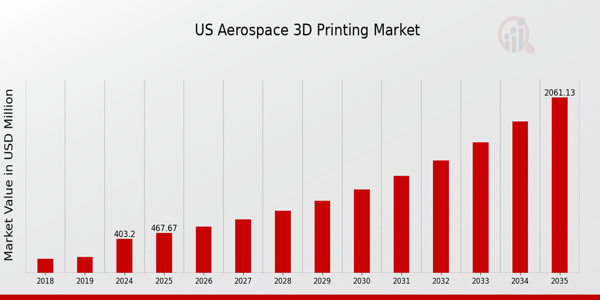
Source: Primary Research, Secondary Research, MRFR Database and Analyst Review
Key US Aerospace 3D Printing Market Trends Highlighted
The US Aerospace 3D Printing Market is experiencing significant growth driven by several key factors. One major driver is the increasing demand for lightweight components that can enhance fuel efficiency and performance in aerospace applications. Companies in the US are investing in advanced materials and technologies to produce parts that meet stringent safety and regulatory standards, while also reducing production time and costs. The push towards sustainability in aviation is also propelling interest in 3D printing, as it allows for greater material efficiency and less waste. Opportunities in the market can be capitalized on by focusing on the customization and rapid prototyping of parts.The ability to quickly produce specialized components tailored for specific aircraft designs is appealing to manufacturers looking to differentiate themselves. Additionally, collaborations between aerospace companies and technology firms are paving the way for innovative solutions and improved processes in 3D printing. In recent times, there has been a notable trend toward certification of 3D printed parts by regulatory bodies such as the Federal Aviation Administration (FAA). This is crucial for enabling wider adoption within the aerospace sector, as companies seek to ensure compliance with safety standards. Furthermore, increased investment in research and development by US organizations, including partnerships with universities and research institutions, is fostering an environment of innovation.The government is also encouraging the use of advanced manufacturing techniques to maintain competitiveness in the aerospace industry, which is a significant aspect of the US economy. This sets a strong foundation for continued advancements in the aerospace 3D printing landscape.
US Aerospace 3D Printing Market Drivers
Increasing Demand for Lightweight Components
The US Aerospace 3D Printing Market Industry is experiencing significant growth due to the increasing demand for lightweight components in aerospace applications. According to the National Aeronautics and Space Administration (NASA), the aerospace sector is targeting a reduction in the weight of aircraft components by approximately 20% over the next decade. This shift is primarily motivated by the need to enhance fuel efficiency and reduce emissions, which align with global sustainability goals.Organizations like Boeing and Lockheed Martin are now leveraging 3D printing technologies to innovate and produce complex geometries that help achieve these weight reductions. The adoption of 3D printing not only aids in producing lighter components but also allows for rapid prototyping and reduced manufacturing time, thereby contributing to lower operational costs and improved performance in the aerospace sector.
Cost Reduction in Prototyping and Production
Cost reduction is a fundamental driver for the growth of the US Aerospace 3D Printing Market Industry. According to the United States Department of Defense (DoD), additive manufacturing technologies can lower production costs by 30% to 50% compared to traditional manufacturing methods. This significant cost advantage is prompting aerospace companies to invest heavily in 3D printing, allowing them to produce components on-demand, thereby minimizing excess inventory and warehousing costs.Major players like General Electric and Northrop Grumman have reported substantial savings in both time and resources by integrating 3D printing into their production processes, which showcases the economic benefits of this technology in enhancing profitability.
Customization and Complex Design Capabilities
The capability of 3D printing to create highly customized and complex designs is driving the growth of the US Aerospace 3D Printing Market Industry. The capability to produce intricate structures that are not feasible with traditional manufacturing techniques is crucial in aerospace applications, where tailored components can significantly enhance performance. The Federal Aviation Administration (FAA) has highlighted that the ability to rapidly prototype and manufacture customized parts can lead to advancements in aircraft performance and safety.Organizations like Airbus are utilizing 3D printing to develop parts that are uniquely designed for specific aircraft models, optimizing the overall efficiency and operational effectiveness of their fleets.
Sustainability Initiatives and Regulatory Support
Sustainability initiatives and regulatory support are becoming substantial drivers for the growth of the US Aerospace 3D Printing Market Industry. The US government is actively promoting the use of additive manufacturing technologies to reduce the aerospace industry's carbon footprint. The Environmental Protection Agency (EPA) has set ambitious standards for emissions reductions, compelling aerospace manufacturers to explore innovative solutions that 3D printing provides.Companies such as Raytheon Technologies are leading the way by focusing on sustainable manufacturing practices that meet regulatory guidelines, thereby ensuring not only compliance but also a competitive advantage in the evolving marketplace focused on sustainability.
US Aerospace 3D Printing Market Segment Insights
Aerospace 3D Printing Market Technology Insights
The US Aerospace 3D Printing Market, particularly in the Technology segment, represents a dynamic landscape where advanced manufacturing techniques are fostering innovation and efficiency in the aerospace sector. Among the various technologies, Stereolithography (SLA) stands out for its capability to produce high-resolution parts quickly, making it ideal for prototyping and producing detailed components. Selective Laser Sintering (SLS) is significant as it allows for the production of robust, functional parts from a variety of materials, which is essential for the rigorous requirements of aerospace applications.Direct Metal Laser Sintering (DMLS) plays a crucial role by enabling the creation of complex geometries from metal powders, thereby reducing material waste and allowing for the design of lighter parts that improve fuel efficiency. Fused Deposition Modeling (FDM) is widely used for creating cost-effective prototypes and tooling fixtures, thus enhancing the overall manufacturing process and reducing lead times. Continuous Liquid Interface Production (CLIP) is gaining traction for its speed and ability to produce continuous, isotropic parts, allowing aerospace manufacturers to push boundaries in design and functionality.This segmentation reflects the growing trend of adopting additive manufacturing technologies, which not only support the production of lighter and more efficient aircraft components but also reduce lead times and production costs. The increasing focus on sustainability and material optimization within the aerospace industry is driving the adoption of these innovative technologies, generating interest and investment. Overall, the Technology segment of the US Aerospace 3D Printing Market stands at the forefront of the industry's shift towards more efficient and adaptable manufacturing processes, catering to the evolving needs of the aerospace sector for durability, compliance, and rapid production capabilities.
Source: Primary Research, Secondary Research, MRFR Database and Analyst Review
Aerospace 3D Printing Market Application Insights
The Application segment of the US Aerospace 3D Printing Market encompasses critical areas such as Engine components, Structural parts, and Space components, highlighting the diverse uses of 3D printing technology within the aerospace industry. This segmentation is essential as it addresses the specific requirements of each area, from the production of lightweight yet durable engine parts to the complex geometries needed in structural frameworks. Engine components often demand precision and high thermal resistance, making 3D printing a viable solution for innovation in turbine design and fuel efficiency.The Structural category significantly benefits from additive manufacturing's ability to create complex shapes that reduce weight, thus enhancing overall aircraft performance and fuel consumption. Space Components represent a rapidly evolving frontier where 3D printing plays a pivotal role in enabling the production of parts for spacecraft and satellite applications, directly supporting mission efficiency and reducing lead times. Overall, the Application segment underscores the transformative potential of 3D printing in meeting the rigorous standards and demands of the aerospace sector, contributing to increased operational efficiency and reduced costs.As the market progresses, the focus on these specific applications is likely to drive further advancements and wider adoption of 3D printing technologies in the US aerospace industry.
Aerospace 3D Printing Market Industry Insights
The US Aerospace 3D Printing Market is experiencing notable growth, driven by advancements in additive manufacturing technologies that enhance production efficiency and reduce costs in the aerospace sector. Within this market, the Aircraft segment is of paramount importance, as it addresses the increasing demand for lightweight and complex components, contributing to fuel savings and improved performance. The Spacecraft segment plays a critical role as well, focusing on the need for rapid prototyping and customization of parts for space missions, where innovation is essential for achieving mission success.Additionally, the UAV segment is rapidly gaining traction due to the surge in drone applications for commercial and military purposes, emphasizing the significance of 3D printing in creating specialized components that are lightweight yet robust. Each of these areas showcases the US Aerospace 3D Printing Market's potential to meet the evolving demands of the industry while facilitating improvements in efficiency and sustainability. Overall, market trends indicate that as research and development continue to evolve, the integration of 3D printing in aerospace applications will likely enhance product innovation and operational capabilities, aligning with the broader goals of the US aerospace industry.
US Aerospace 3D Printing Market Key Players and Competitive Insights
The competitive insights of the US Aerospace 3D Printing Market reveal a dynamic landscape characterized by innovation and rapid technological advancement. As the manufacturing industry continues to prioritize efficiency, customization, and sustainability, 3D printing has emerged as a significant force within the aerospace sector. The market is driven by an increasing demand for lightweight components, the need for complex geometries that traditional manufacturing cannot achieve, and the desire for reduced waste in the production process. Major players are investing in research and development to enhance material capabilities and printing technologies, enabling them to offer tailored solutions that meet the unique demands of aerospace applications. This competitive atmosphere necessitates companies to adapt swiftly to technological changes and market trends while forming strategic partnerships and collaborations to maintain their edge.Raytheon Technologies has established a formidable presence in the US Aerospace 3D Printing Market through its commitment to advancing additive manufacturing technologies. The company leverages its extensive expertise in defense and aerospace solutions to innovate in the realm of 3D printing, focusing on aspects such as rapid prototyping and the production of intricate parts. Raytheon Technologies' strengths lie in its robust research capabilities and a diverse portfolio that spans various segments of the aerospace industry. This allows the company to not only address the immediate needs of military and commercial customers but also to push the boundaries of what is possible in aerospace manufacturing. With state-of-the-art facilities and a skilled workforce, Raytheon Technologies is well-positioned to capitalize on the growing demand for advanced manufacturing techniques in the aerospace sector.Boeing stands out as a powerful entity in the US Aerospace 3D Printing Market, offering a wide range of products and services that benefit from additive manufacturing technologies. The company is renowned for its advanced aircraft models and innovative solutions, utilizing 3D printing to streamline production processes and enhance the performance of various components. Boeing has made significant investments in 3D printing capabilities, focusing on high-strength, lightweight parts that meet the stringent demands of commercial and military aerospace applications. The company's strengths are particularly evident in its strategy of integrating 3D printing into the broader manufacturing process, which allows for increased efficiency and reduced lead times. Furthermore, Boeing has engaged in strategic mergers and acquisitions, positioning itself to bolster its capabilities in additive manufacturing and expand its market presence in the aerospace sector. This forward-thinking approach enables Boeing to harness the potential of 3D printing to maintain its competitive advantages within the US aerospace landscape.
Key Companies in the US Aerospace 3D Printing Market Include
US Aerospace 3D Printing Market Industry Developments
Recent developments in the US Aerospace 3D Printing Market have shown significant advancements among key players like Raytheon Technologies, Boeing, and Lockheed Martin, focusing on enhancing production efficiency and reducing costs. The increasing adoption of additive manufacturing techniques is evident with companies like 3D Systems, Renishaw, and Stratasys innovating robust materials for aerospace applications. In October 2023, Northrop Grumman announced a strategic partnership with General Electric to collaboratively develop next-generation components using 3D printing technologies, aiming to streamline supply chains and improve sustainability.The market has also seen notable mergers and acquisitions; in September 2023, Honeywell acquired a majority stake in a 3D printing firm specializing in advanced aerospace materials, which underscores the growing importance of 3D printing in aerospace applications. Recent growth in the sector is reflected in valuations, particularly for companies like HP and EOS, which have reported increased revenues driven by their aerospace solutions. Over the past 2-3 years, the US has witnessed a surge in federal investments to promote Research and Development in aerospace technologies, focusing heavily on 3D printing to meet defense and commercial needs effectively.
US Aerospace 3D Printing Market Segmentation Insights
Aerospace 3D Printing Market Technology Outlook
- Selective Laser Sintering (SLS)
- Direct Metal Laser Sintering (DMLS)
- Fused Deposition Modeling (FDM)
- Continuous Liquid Interface Production (CLIP)
Aerospace 3D Printing Market Application Outlook
Aerospace 3D Printing Market Industry Outlook
Report Scope:
Report Attribute/Metric Source: |
Details |
MARKET SIZE 2018 |
336.0(USD Million) |
MARKET SIZE 2024 |
403.2(USD Million) |
MARKET SIZE 2035 |
2061.16(USD Million) |
COMPOUND ANNUAL GROWTH RATE (CAGR) |
15.989% (2025 - 2035) |
REPORT COVERAGE |
Revenue Forecast, Competitive Landscape, Growth Factors, and Trends |
BASE YEAR |
2024 |
MARKET FORECAST PERIOD |
2025 - 2035 |
HISTORICAL DATA |
2019 - 2024 |
MARKET FORECAST UNITS |
USD Million |
KEY COMPANIES PROFILED |
Raytheon Technologies, Boeing, Lockheed Martin, Renishaw, ExOne, 3D Systems, Materialise, Stratasys, Northrop Grumman, General Electric, HP, Honeywell, Siemens, EOS |
SEGMENTS COVERED |
Technology, Application, Industry |
KEY MARKET OPPORTUNITIES |
Additive manufacturing cost reduction, Lightweight components production, Custom tooling solutions, Rapid prototyping advancements, Supply chain efficiency improvements |
KEY MARKET DYNAMICS |
increased demand for lightweight components, advancements in material technologies, regulatory compliance and certifications, cost reduction in manufacturing, customization and rapid prototyping capabilities |
COUNTRIES COVERED |
US |
Frequently Asked Questions (FAQ) :
The US Aerospace 3D Printing Market is expected to be valued at 403.2 million USD in 2024.
By 2035, the market is projected to reach a value of 2061.16 million USD.
The expected CAGR for the US Aerospace 3D Printing Market during this period is 15.989%.
The Direct Metal Laser Sintering (DMLS) segment is expected to dominate the market with a value of 653.42 million USD by 2035.
The Selective Laser Sintering (SLS) segment is projected to be valued at 430.4 million USD in 2035.
Major players include Raytheon Technologies, Boeing, Lockheed Martin, and General Electric among others.
The market value for Stereolithography (SLA) technology is anticipated to be 60.0 million USD in 2024.
Challenges may include regulatory hurdles and the high costs associated with advanced 3D printing technologies.
Emerging trends such as advancements in materials and increasing adoption in production processes present significant growth opportunities.
The Fused Deposition Modeling (FDM) segment is expected to reach a market value of 514.51 million USD by 2035.