Injection Molding Machinery Market Summary
As per Market Research Future Analysis, the Global Injection Molding Machinery Market was valued at USD 10.28 Billion in 2023 and is projected to reach USD 13.95 Billion by 2032, growing at a CAGR of 3.40% from 2024 to 2032. Key drivers include increasing energy efficiency consciousness and rising demand for large-tonnage injection molding devices. The market is segmented by type, with hydraulic machines leading at 43% market revenue in 2022. The automotive sector is the largest end-user, accounting for 32% of market revenue. North America is expected to dominate the market due to advanced manufacturing technologies.
Key Market Trends & Highlights
The injection molding machinery market is witnessing significant trends driven by energy efficiency and technological advancements.
- Market Size in 2023: USD 10.28 Billion.
- Hydraulic machines accounted for 43% of market revenue in 2022.
- Automotive sector represented 32% of market revenue in 2022.
- Less than 200 tons clamping force segment generated 46% of market revenue in 2022.
Market Size & Forecast
2023 Market Size: USD 10.28 Billion
2024 Market Size: USD 10.68 Billion
2032 Market Size: USD 13.95 Billion
CAGR (2024-2032): 3.40%
Largest Regional Market Share in 2024: North America
Major Players
HAITIAN International (China), SUMITOMO Heavy Industries (Japan), JAPAN Steel Works (Japan), Chen Hsong Holdings (Hong Kong), Hillenbrand Inc. (US), Dongshin Hydraulic (South Korea)
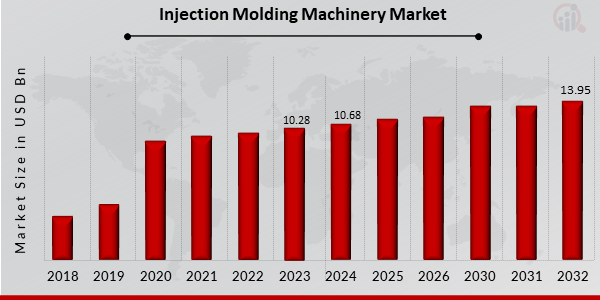
Source Secondary Research, Primary Research, Market Research Future Database, and Analyst Review
Injection Molding Machinery Market Trends
Growing energy efficiency consciousness is driving the market growth
The rising energy efficiency consciousness drives Market CAGRÂ for injection molding machinery. Globally, there is a rising awareness of the necessity for energy conservation, driving consumer interest in all-electric machinery, particularly electric injection molding machines. Electric motors provide a very environmentally friendly machine since they are only activated when mobility is required. Furthermore, the novel energy retrieval system absorbs and stores kinetic energy, which can power the machine. The primary reasons are its numerous benefits, which include minimal upkeep eliminating the need for oil for sanitation, savings on electricity, enhanced accuracy and versatility, and fast speed.
Regarding cost-effectiveness, cycle time reductions, efficiency, dependability, and reuse ability, all-electric injection molding machines surpass hHydraulic Cylinder . They use digital electronic controls and conserve up to 70% more energy than traditional hydraulic machines. As a result, many of these molding machines' elements are operated manually.
Additionally, massive-tonnage injection molding devices are in high demand, which are utilized to produce massive molded components for automotive, appliance, and business uses. In the past, due to plant construction expenses, the need for injection molding machines was limited to 400 tons, with 500 presses constituting the upper limit. The need has shifted over time. Large components are in high demand. Machine makers' capacity to design a big energy-efficient machine with a short cycle time has improved.
The effect of COVID-19 comprises a shortage of subcontractors and products, supply chain disruptions, and contractual dismissals to reduce costs. This market saw declines in growth throughout the epidemic, but it is expected to rebound swiftly when economic activity resumes. Before the COVID-19 epidemic, geopolitical factors drove regional and regional raw material sourcing, leading to short production runs and a diversified product line. Growing automation usage and rising demand for vehicles and consumer items will propel the injection molding machine market forward.
For instance, according to the Plastics Industries Organization, the delivery of massive machinery climbed much more than the shipment of small machines. Large injection molding machines provide businesses with excellent business potential in various areas, including sports, agriculture, and automobiles. Thus, it is anticipated that demand for Injection Molding Machinery will increase throughout the projected timeframe due to the rising Energy Efficiency Consciousness. Thus, driving the Injection molding machine market revenue.
Injection Molding Machinery Market Segment Insights
Injection Molding Machinery Type Insights
The Injection Molding Machinery market segmentation, based on type, includes Electric, Hydraulic Cylinder, and Hybrid Machines. The hydraulic segment dominated the market, accounting for 43% of market revenue (USD 4.3 Billion) in 2022. The capacity to manufacture huge quantities of parts, complex components for the automotive sector, less expensive initial manufacturing of precise molds, greater corrosion and wear obstruction of hydraulic parts, along with widespread application in the automobiles, marine, and aerospace sectors where heaviest force needs to be met are all expected to drive market growth.
Injection Molding Machinery Clamping Force Insights
Based on Clamping forces, the global injection press market segmentation includes less than 200 tons force, 200 to 500 tons force, and more than 500 tons force. The less than 200 tons force category generated the highest market revenue of about 46% (USD 4.6 billion) in 2022. This is due to a growth in the number of middle and small-sized manufacturing firms in industrialized and emerging countries.
Figure 1 Injection Molding Machinery Market by Clamping force, 2022 & 2032 (USD Billion)

Source Secondary Research, Primary Research, Market Research Future Database, and Analyst Review
Injection Molding Machinery Material Insights
The Injection Molding Machinery market segmentation, based on Material, includes rubber, metal, plastic, and ceramics. The plastic Extrusion Machine segment dominated the market, accounting for 37% of market revenue (USD 3.7 Billion) in 2022. This is due to the rapid rise in plastic components in the automobile sector due to their lightness and low cost.
Injection Molding Machinery End-Use Insights
Based on End-Use, the Injection Molding Machinery market segmentation includes automotive, consumer goods, health care, electricals & electronics. The automotive segment dominated the market, accounting for 32% of market revenue (USD 3.2 Billion) in 2022. Increased automobile output and increased need for compact automotive parts will drive market expansion.
Injection Molding Machinery Regional Insights
By region, the research provides market insights into North America, Europe, Asia-Pacific, and the Rest of the World. The North American Injection Molding Machinery market area will dominate this market during the projected timeframe, as manufacturing firms are heavily utilizing sophisticated technology to improve their company operations, boosting the market growth in the North American region.
Further, the major countries studied in the market report are the US, Canada, German, France, the UK, Italy, Spain, China, Japan, India, Australia, South Korea, and Brazil.
Figure 2 Injection Molding Machinery Market Share by Region 2022 (USD Billion)

Source Secondary Research, Primary Research, Market Research Future Database, and Analyst Review
Europe region’s Injection Molding Machinery market is expected to grow quickly during the projected timeframe owing to the rise in the automobile sector. The region's expansion is further fueled by rising interest in the electric car sector. Further, the German Injection Molding Machinery market holds the largest market share, and the UK Injection Molding Machinery market is expected to grow and expand significantly in the European region during the projected timeframe.
The Asia-Pacific Injection, Molding Machinery Market accounts for the second-highest market share during the projected timeframe. The area is regarded as one of the world's most significant contributors to this market. Expanding businesses in this area is a significant factor driving market growth. Moreover, China’s Injection Molding Machinery market dominates the market share, and the Indian Injection Molding Machinery market is expected to expand and grow steadily in the Asia-Pacific region during the projected timeframe.
Injection Molding Machinery Key Market Players & Competitive Insights
Leading market players invested heavily in research and Development (R&D) to scale up their manufacturing units and develop technologically advanced solutions, which will help the Injection Molding Machinery market grow worldwide. Market participants are also undertaking various organic or inorganic strategic approaches to strengthen and expand their global footprint, with significant market developments including new product portfolios, contractual deals, mergers and acquisitions, capital expenditure, higher investments, and strategic alliances with other organizations.
Businesses are also coming up with marketing strategies such as digital marketing, social media influencing, and content marketing to increase their scope of profit earnings. The Injection Molding Machinery industry must offer cost-effective and sustainable options to survive in a highly fragmented and dynamic market climate.
Manufacturing locally to minimize operational expenses and offer aftermarket services to customers is one of the critical business strategies organizations use in the global Injection Molding Machinery industry to benefit customers and capture untapped market share and revenue. The Injection Molding Machinery industry has recently offered significant advantages to the Industrial Automation & Equipment industry. Moreover, more industry participants are utilizing and adopting cutting-edge technology has grown substantially.
Major players in the Plastic Injection Molding Machine market, including HAITIAN International (China), SUMITOMO Heavy Industries (Japan), JAPAN Steel Works (Japan), Chen Hsong Holdings (Hong Kong), Hillenbrand Inc.(US), Dongshin Hydraulic (South Korea), are attempting to expand market share and demand by investing in R&D operations to produce sustainable and affordable solutions.
Otto Hofstetter is a 100% family-owned worldwide premier mold and die producer. It provides full help, from consultation using design and teaching to professional after-sales service. Otto Hofstetter, located in Switzerland, is expanding its line of goods, offering specialist injection molds in March 2021. The firm has included various goods to strengthen its initiatives in the medical technology and drug sectors.
Nolato AB is a holding corporation whose companies specialize in developing and producing injection molded goods and components. The company is a polymer-based product specialist Nolato supplies manufacturers, cell phones and additional telecommunications providers, and healthcare businesses. The business is active in the European Union, the USA, and the APAC region. In February 2021, Nolato Company finished completing the setup of 75-tonne molding equipment at Avenue, its subsidiary organization. The molding equipment will be used to produce mold precision items that are still in the development stage.
Key Companies in the Injection Molding Machinery market include
- HAITIAN International (China)
- SUMITOMO Heavy Industries (Japan)
- Chen Hsong Holdings (Hong Kong)
- Dongshin Hydraulic (South Korea)
Injection Molding Machinery Industry Developments
March 2024- The first medical-specific all-electric injection molding machine from Shibaura Machine Company, America, will be launched to the North American market during Plastec West 2024. The Key Accounts Sales Manager for the Medical Casting/Molding Division at Shibaura, Chad Clawson, said that for many years, medical device producers have been using their general-purpose ECSXIII machine to mold a range of products.Â
He further added that their new medical-specific machine provides the same speed and functionality as other ECSXIII models, with improvements that are ideal for medical molding and cleanroom environments. At Plastec West, Shibaura will utilize the latest EC110SXIII medical machine to manufacture medical pipettes. Completely incorporated with the EC110SXIII will be a Mold-Masters hot runner controller and Mold-Masters water manifold system, which are available as optional add-ons.
The brand-new addition to Shibaura's popular ECSXIII series of all-electrics, the latest medical machine offers fast injection speeds and dry cycle times, guarantees longer mold life and provides uniform clamping force for better flexibility, productivity, and versatility. The machine also has the same user-friendly V70 controller built into all ECSXIII models, making it simple for operators to lower mold set-up time, enhance cycle times, examine part defects, troubleshoot defects, and more.Â
Comprised with the new machine is a full-year subscription to machiNetCloud, Shibaura's absolute industrial IoT service offering producers remote, real-time access to machine data so they can supervise authorized processes for molded components anytime from any location. The latest medical-specific EC110SXIII is at present available in 110 US tons, with bigger sizes to be available in the future.
December 2023- LS Mtron Injection Molding Machine continues to expand in North America. In just the last few months, the organization has started a new business unit in Mexico and has appointed several sales and service personnel in the USA to keep up with its rapid growth.
February 2023
Japanese company Sumitomo Heavy Industries Ltd. (SHI) has unveiled the 20-ton iM18E tiny hybrid injection molding machine, which has a small 88 by 30 in. footprint. The iM18E has a maximum injection speed of 600 mm/sec and was specifically created for molding connections, precise gears, and other electronic parts. According to a business spokeswoman, the equipment will currently only be available in Japan and other Asian markets.
According to SHI, the iM18E takes up about 21% less space than the SE18DUZ, the company's similar model. Thanks to a redesigned injection unit and a machine frame that enables auxiliary equipment to be stored under the machine, the iM18E requires significantly less floor space.
The iM18E has an electronic plasticizing unit with a low-inertia servomotor and a hydraulic direct-pressure clamp. SHI claims that the iM18E's shot-to-shot weight variance is reduced to around one-third of that of an equivalent hydraulic machine when driven by the ISCII direct-drive system. According to reports, the hybrid design uses 50% less energy than identical hydraulic machinery.
April 2023
JSW has introduced the JLM3000-MGIIeL, the largest magnesium injection molding machine in the world, following the 1,300-tonne mold clamping force of the JLM-MGIIe series, which uses the Thixomolding technology,
The third generation of JSW's magnesium injection molding machines is the JLM-MGIIe series. Four models—the JLM280-MGIIe, JLM650-MGIIe, JLM850-MGIIe, and JLM1300-MGIIeL—have been introduced, delivered, and warmly welcomed by customers. This time, we created a larger model in response to the needs of the market.
JLM3000-MGIIeL utilizes the electrification technology acquired in plastic injection molding machines in addition to the extensive expertise in magnesium injection molding machines amassed over the course of 30 years and introduces a new electric mold clamping device in pursuit of environmental performance.
The new technology aids the customers in keeping their production line clean and environmentally friendly by enabling high-precision, high-quality molding of big magnesium parts, which had previously been challenging to use the Thixomolding method.
June 2021Â Boddingtons, a leading medical equipment maker, has opted to add a dual shot molding cell within its factory to increase its manufacturing capacity.
March 2021Â Otto Hofstetter, located in Switzerland, is expanding its line of goods offering specialist injection molds. The firm has included various goods to strengthen its initiatives in the medical technology and drug sectors.
February 2021Â Nolato Company has completed the setup of 75-tonne molding equipment at Avenue, its subsidiary organization. The molding equipment will be used to produce mold precision items that are still in the development stage.
Injection Molding Machinery Market Segmentation
Injection Molding Machinery Type Outlook
Injection Molding Machinery Clamping force Outlook
- Less than 200 tons of force
- More than 500 tons of force
Injection Molding Machinery Material Outlook
Injection Molding Machinery End-User Outlook
- Electricals & Electronics
Injection Molding Machinery Regional Outlook
Report Attribute/Metric |
Details |
Market Size 2023 |
USD 10.28 Billion |
Market Size 2024 |
USD 10.68 Billion |
Market Size 2032 |
USD 13.95 Billion |
Compound Annual Growth Rate (CAGR) |
3.40% (2024-2032) |
Base Year |
2023 |
Market Forecast Period |
2024-2032 |
Historical Data |
2018- 2022 |
Market Forecast Units |
Value (USD Billion) |
Report Coverage |
Revenue Forecast, Market Competitive Landscape, Growth Factors, and Trends |
Segments Covered |
Type, Clamping force, Material, End-Use, and Region |
Geographies Covered |
North America, Europe, Asia Pacific, and the Rest of the World |
Countries Covered |
The US, Canada, German, France, UK, Italy, Spain, China, Japan, India, Australia, South Korea, and Brazil |
Key Companies Profiled |
 HAITIAN International (China), SUMITOMO Heavy Industries (Japan), JAPAN Steel Works (Japan), Chen Hsong Holdings (Hong Kong), Hillenbrand Inc.(US), Dongshin Hydraulic (South Korea) |
Key Market Opportunities |
The requirement for Large-Tonnage Injection molding devices is a key market opportunity. |
Key Market Dynamics |
Increasing Energy Efficiency Consciousness |
Injection Molding Machinery Market Highlights:
Frequently Asked Questions (FAQ):
The Injection Molding Machinery market size was valued at USD 10.28 Billion in 2023.
The global market is projected to grow at a CAGR of 3.40% during the forecast period, 2024-2032.
North America had the largest share of the global market
The key players in the market are HAITIAN International (China), SUMITOMO Heavy Industries (Japan), JAPAN Steel Works (Japan), Chen Hsong Holdings (Hong Kong), Hillenbrand Inc.(US), Dongshin Hydraulic (South Korea).
The Hydraulic category dominated the market in 2022.
The Less than 200 tons force had the largest share in the global market.