Semiconductor Bonding Market Summary
As per MRFR Analysis, the Global Semiconductor Bonding Market was valued at USD 0.7 billion in 2021 and is projected to grow from USD 0.72 billion in 2022 to USD 0.89 billion by 2030, with a CAGR of 3.11% during the forecast period. Key drivers include the rising demand for miniature electronic components and electric vehicles. The adoption of stacked die technology in IoT devices is also enhancing market growth, as it allows for compact designs and improved semiconductor processes. The increasing production of 5G devices and the demand for wearable technology further contribute to market expansion.
Key Market Trends & Highlights
Key trends driving the Semiconductor Bonding Market include technological advancements and increasing applications in various sectors.
- The Semiconductor Bonding market is expected to reach USD 0.89 billion by 2030.
- The Asia-Pacific region is projected to grow at the fastest CAGR from 2022 to 2030.
- North America accounted for USD 0.30 billion in 2021, driven by electric vehicle demand.
- Europe aims to produce advanced 2 nm chips by 2030, enhancing market opportunities.
Market Size & Forecast
2021 Market Size: USD 0.7 Billion
2022 Market Size: USD 0.72 Billion
2030 Market Size: USD 0.89 Billion
CAGR (2022-2030): 3.11%
Largest Regional Market Share in 2021: North America.
Major Players
Key players include BE Semiconductor Industries N.V., ASM Pacific Technology Ltd, Kulicke & Soffa, and Panasonic.
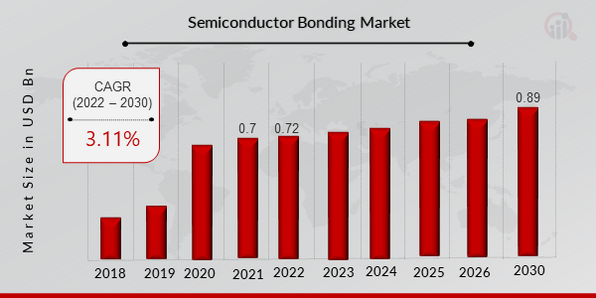
Source: Secondary Research, Primary Research, MRFR Database and Analyst Review
Semiconductor Bonding Market Trends
- Rising Adoption of Stacked Die Technology in IoT Devices to boost market growth
The use of stacked chips greatly improves the semiconductor design process. Stacked die technology is used to create small final designs. One of the main drivers of progress in stacked die technology is handheld electronic devices. Also, the live tracking IoT gadget does not have a large size. Accelerate time to market by reducing design effort and increasing your chances of success the first time. Therefore, increasing adoption of stacked die technology in IoT devices will increase the demand for semiconductor bonding solutions in the market. OEMs operating in the semiconductor sector are reaping the benefits of his IoT beyond connectivity. Sensors, RFID tags, smart beacons, smart meters, and power distribution control systems are IoT devices and technologies that are increasingly used in a variety of applications. B. Building and Home Automation, Connected Logistics, Smart Manufacturing, Smart Retail, Smart Mobility, Smart Transportation. IoT devices use semiconductor bonding technology to compactly attach multiple stacked chips to a substrate. This will lead to the growth of the semiconductor bonding market.
The amount of 5G devices produced increased from 251 million units in 2020 to 556 million in 2021, according to data from Semiconductor Today. Furthermore, it is predicted that the semiconductor bonding market would rise over the course of the forecast period due to the rising need for wearable technology, smartphones, and 5G services. Therefore, such high demand and new product launches has enhanced the Semiconductor Bonding market CAGR across the globe in the recent years.
Additionally, OEMs working in the semiconductor industry are making use of IoT's advantages beyond connection. Smart manufacturing, smart retail, connected logistics, smart home automation, smart mobility, and smart transportation are just a few of the IoT applications that are increasingly using sensors, RFID tags, smart beacons, smart metres, and distribution management systems. The semiconductor bonding market will expand because IoT devices use semiconductor bonding techniques to compactly attach several stacked dies to substrates. However, increasing spending on research and development activities is another factor driving the growth of the Semiconductor Bonding market revenue.
Semiconductor Bonding Market Segment Insights
Semiconductor on Process Type Insights
The Semiconductor Bonding market segmentation, based on process type, includes die-to-die bonding, die-to-wafer bonding, and wafer-to-wafer bonding. A bonding requires a controlled combination of the right materials and implements a combination of conditions such as force, pressure and high temperature required for the bonding process. Wafer bonders can generally be considered suitable for maintaining proper alignment between the two surfaces to be bonded. As a result, wafer bonders are complex systems that require a high level of precision and control.
January 2021 In order to develop die-to-wafer hybrid bonding solutions for 3D-IC and heterogeneous integration applications, ASM PACIFIC TECHNOLOGY (ASMPT) and EV GROUP (EVG) joined forces. Chiplets are an advanced packaging technology that combines chips with various process nodes to power new applications like 5G, high-performance computing (HPC), and artificial intelligence. Die-to-wafer hybrid bonding is an essential step in the redesign of system-on-chip (SoC) devices to 3D stacked chips using chiplet technology, which combines chips from various process nodes into sophisticated packaging systems that can power new applications like 5G, HPC, and artificial intelligence (AI).
Semiconductor Bonding On Technology Insights
The Semiconductor Bonding market data has been bifurcated by technology into die bonding, epoxy die bonding, eutectic die bonding, flip-chip attachment, and hybrid bonding. Die bonding can be defined as the application of semiconductor materials to the next level of connectivity, whether physical or circuit board. This is known in the industry as die placement, die connecting, or die bonding. Even with the same goals, die bonding processes and hardware are very different, depending on features and functions, cost, performance, volume, historical or existing product life criteria, and required durability.
September 2021 Palomar Technologies launched a new Palomar 3880-II Die Bonder.
April 2021 In order to enable the considerable intensity diversified inclusion of ultra-thin dies up to 300 mm base wafer, ASM Pacific Technology announced three new production techniques utilising X-Micro Celeprint's Transfer Publishing and ASM AMICRA's good repeatability die bonding technology.
Figure 2: Semiconductor Bonding Market, by Technology, 2021 & 2030 (USD Billion)
Source: Secondary Research, Primary Research, MRFR Database and Analyst Review
Semiconductor Bonding Regional Insights
By Region, the study provides the market insights for Semiconductor Bonding into North America, Europe, Asia-Pacific and Rest of the World. North America Semiconductor Bonding market accounted for USD 0.30 billion in 2021 and is expected to exhibit a significant CAGR growth during the study period. This is attributed to the rising demand for electric and hybrid vehicles across the region.
Further, the major countries studied in the market report for Semiconductor Bonding are The U.S, Canada, Germany, France, UK, Italy, Spain, China, Japan, India, Australia, South Korea, and Brazil.
Figure 3: SEMICONDUCTOR BONDING MARKET SHARE BY REGION 2021 (%)
Source: Secondary Research, Primary Research, MRFR Database and Analyst Review
Europe semiconductor bonding market accounts for the second-largest market share. According to an EU report, Europe aims to produce the next generation of state-of-the-art chips (2 nm) by 2030. European semiconductor companies such as Infineon Technologies and ASML Holding invest heavily in research and development to develop advanced semiconductor bonding solutions. In addition, the growing number of semiconductor junction start-ups in Europe is expected to provide new opportunities for digital technologies in the semiconductor industry. Moreover, increasing adoption of electric vehicles in European countries, supported by government green initiatives, is expected to contribute to the growth of the semiconductor junction market. For instance, the UK government has set a target for all electric vehicles to meet environmental sustainability standards by 2030. Further, the Germany semiconductor bonding market held the largest market share, and the UK semiconductor bonding market was the fastest growing market in the European region.
The Asia-Pacific Semiconductor Bonding Market is expected to grow at the fastest CAGR from 2022 to 2030. This is due to major domestic organizations and government agencies are investing resources intensively in technology to develop next-generation semiconductor bonding solutions such as gold wire bonding and semiconductor wafer bonding solutions. Moreover, China semiconductor bonding market held the largest market share, and the India semiconductor bonding market was the fastest growing market in the North American region.
Semiconductor Bonding Key Market Players & Competitive Insights
Major market players are spending a lot of money on R&D to increase their product lines, which will help the Semiconductor Bonding market grow even more. Market participants are also taking a range of strategic initiatives to grow their worldwide footprint, with key market developments such as new product launches, contractual agreements, mergers and acquisitions, increased investments, and collaboration with other organizations. Competitors in the semiconductor bonding industry must offer cost-effective items to expand and survive in an increasingly competitive and rising market environment.
One of the primary business strategies adopted by manufacturers in the semiconductor bonding industry to benefit to the customers and expand the market sector is to manufacture locally to reduce operating costs. In recent years, semiconductor bonding industry has provided advance product with significant benefits. The semiconductor bonding market major player such as BE Semiconductor Industries N.V., ASM Pacific Technology Ltd, Kulicke & Soffa, Panasonic, and others are working to expand the market demand by investing in research and development activities.
BE Semiconductor Industries N.V. (Besi) develops assembly processes and equipment for leadframe, substrate and wafer level packaging applications in a wide range of end-user markets including electronics, mobile internet, cloud server, computing, automotive, industrial, LED and solar energy. In October 2020, The companies BE Semiconductor Industries N.V. and Applied Materials, Inc. The industry's first full and tested equipment solution for die-based hybrid bonding, a cutting-edge chip-to-chip interconnect technology that enables heterogeneous chip and subsystem designs for applications including high-performance computing, artificial intelligence, and 5G, was announced by (Besi).
Also, ASMPT's products range from wafer deposition and laser grooving to diverse solutions for molding, assembling and packaging delicate electronic and optical components into a wide range of end-user devices. These include electronics, mobile communications, computers, automotive, industrial and LED (displays)., In April 2021, ASM Pacific Technology introduced three new production processes utilizing X-Micro celeprint's transfer publishing and ASM AMICRA's good reproducibility die bonding technology to allow substantial intensity diverse incorporation of ultra-thin dies up to 300 mm base wafer.
Key Companies in the Semiconductor Bonding market includes
Semiconductor Bonding Industry Developments
November 2023: EV Group (EVG), November 2023, announced the completion of construction works for the next phase of EVG corporate headquarters expansion. A “Manufacturing V” is the largest manufacturing department of EVG, which deals with equipment components and allows for a substantial enlargement of the production floor and warehouse space. The opening at Manufacturing V represents the most recent stage of growth, together with investments made by EVG into processing technologies to satisfy the high demand for its hybrid bonding solutions and other process solutions, as well as process development services in the rapidly growing advanced packaging market and 3D/heterogeneous integration market.
September 2023: MRSI Systems (Mycronic AB), in September 2023, announced a new variant, MRSI-7001HF, being an extension of its well-established MRSI-7001 platform. While bonding, the heated bond head can exert up to 500N forces on its surface. The upper part of the heated bond head also heats up to temperatures as high as 400°C. It makes it the ideal tool for high-force die bonders such as power semiconductor sintering for IC packaging or thermocompression bonders for IC packaging.
November 2022: Impulse Current Bonding was introduced by SÜSS MicroTec SE, which is a novel low-temperature field-assisted bonding technology. Consequently, this released product would enable many MEMS applications faster than ever before while offering creative answers to their technical challenges.
August 2022: Hsinchu-based Industrial Technology Research Institute partnered with EV Group, resulting in innovative heterogeneous integration processes that would be developed jointly by both companies.
June 2022: Tokyo Electron Ltd unveiled Ulucus L – a laser edge trimming system designed specifically for wafer-bonded devices measuring 300. This latest laser control unit is combined with LITHIUS Pro Z - TEL’s world-renowned coater platform.
March 2022: Teramount is a leading provider of scalable solutions for attaching optical fibers to silicon chips. This collaboration would see wafer-level optics implemented by both companies to solve a myriad of silicon photonics, in particular, fiber chip packaging issues. Additionally, EVG’s nanoimprint lithography technology will be supported while Teramount’s PhotonicPlug technology is utilized by them.
Semiconductor Bonding Market Segmentation
Semiconductor Bonding Process Type Outlook
Semiconductor Bonding Technology Outlook
Semiconductor Bonding Regional Outlook
Report Attribute/Metric |
Details |
Market Size 2021 |
USD 0.70 billion |
Market Size 2022 |
USD 0.72 billion |
Market Size 2030 |
USD 0.89 billion |
Compound Annual Growth Rate (CAGR) |
3.11% (2022-2030) |
Base Year |
2021 |
Market Forecast Period |
2022-2030 |
Historical Data |
2018 & 2020 |
Market Forecast Units |
Value (USD Billion) |
Report Coverage |
Revenue Forecast, Market Competitive Landscape, Growth Factors, and Trends |
Segments Covered |
Process Type, Technology, and Region |
Geographies Covered |
North America, Europe, Asia Pacific, and Rest of the World |
Countries Covered |
The U.S, Canada, Germany, France, UK, Italy, Spain, China, Japan, India, Australia, South Korea, and Brazil |
Key Companies Profiled |
BE Semiconductor Industries N.V., ASM Pacific Technology Ltd, Kulicke & Soffa, Panasonic, and others |
Key Market Opportunities |
Rising geriatric population |
Key Market Dynamics |
Increasing burden of chronic diseases such as obesity, diabetes, hypertension, chronic pulmonary diseases, and others. Rising spending on drug development activities |
Semiconductor Bonding Market Highlights:
Frequently Asked Questions (FAQ):
The Semiconductor Bonding market size was valued at USD 0.70 Billion in 2021.
The market for Semiconductor Bonding is projected to grow at a CAGR of 3.11% during the forecast period, 2022-2030.
North America had the largest share in the market for Semiconductor Bonding.
The key players in the market for Semiconductor Bonding are BE Semiconductor Industries N.V., ASM Pacific Technology Ltd, Kulicke & Soffa, Panasonic, and others.
The wafer-to-wafer process type Semiconductor Bonding category dominated the market in 2021.
The die bonding technology had the largest share in the Semiconductor Bonding market.