Pune, India, Nov 2022, MRFR Press Release/Market Research Future has published a Cooked Research Report on the Global Thermoformed Plastics Market.
Thermoformed Plastics Market Highlights
The global thermoformed plastic market is projected to witness significant growth during the review period, exhibiting a CAGR of 4.30%. The market was estimated to be USD 35,086.01 million in 2021 and is expected to reach a value of USD 66.92 Billion by the end of the forecast period (2022-2030).
A plastic sheet is heated to a temperature that makes it flexible, then shaped into a precise shape in a mould and cut to produce a functional product in the industrial process known as thermoforming. The sheet is heated in an oven to a temperature high enough to allow it to be stretched into or onto a mould and chilled to a completed shape, in which case it is referred to as "film" when referring to thinner gauges and specific material types. Vacuum forming is a simplified version of it. Most thermoforming companies recycle their scrap and used plastic by compressing it in a baling machine or feeding it through a granulator (grinder) to create ground flake, which they sell to reprocessing companies or use internally.
Competitive Landscape
The global thermoformed plastics market is characterized by the presence of many regional and local vendors. The market is highly competitive, with all the players competing to gain maximum market share. The increasing thermoformed plastic demand from the healthcare sector is the key driver of the market. The vendors compete based on cost, product quality, and the availability of the products according to the geographies. The vendors must provide cost-effective and high-quality thermoformed plastic to compete in the market. The competitive scenario is fragmented between the tier-1, tier-2, and tier-3 companies, while tier-1 and tier-2 companies hold over 60% of the global market share.
The market players' growth depends on the market and economic conditions, government regulations, and industrial development. Thus, the players should focus on expanding the production capacity to meet the demand and enhance their services. Sonoco Products Company, Fabri-Kal Corporation, Pregis LLC., UFP Technologies, Inc., and Berry Global Group, Inc. are the major companies in the market currently competing in terms of quality, price, and availability. These players are primarily focusing on the development of thermoformed plastic. Although the international players dominate the market, regional and local players with small market shares also have a moderate presence. The international players with a global presence, with established manufacturing units or sales offices, have strengthened their presence across major regions such as North America, Europe, Asia-Pacific, South America, and Middle East & Africa.
Segmentation
By Product Type
- POLYETHYLENE TEREPHTHALATE (PET): An extremely popular material for thermoforming is polyethylene terephthalate. Both bottles and synthetic fibers are made with them. To increase its resistance, PET is thermoformed into a product shape and then dried. PET thermoformed products are resistant to environmental factors including weather and corrosion. This plastic is also among those that are recycled the most. PET contributes to the strength and dependability of electrical devices, photovoltaic panels, switches, and other essential energy components.
- POLYMETHYL METHACRYLATE (PMMAThe polymethyl methacrylate segment held the market share of 3.54% in 2021 and is expected to register the CAGR of 3.62% during the forecast period. Polymethyl Methacrylate (PMMA), commonly referred to as acrylic or acrylic glass, is a transparent and hard thermoplastic substance frequently used as a shatterproof replacement for glass. PMMA has several technical benefits over other transparent polymers (PC, polystyrene, etc.): excellent light transmission, high resilience to UV light and weathering, and unlimited color possibilities. PMMA is produced from monomer methyl methacrylate
- POLYETHYLENE (PE): A thermoplastic plastic made from petroleum called polyethylene (PE) is renowned for having a great strength-to-density ratio. Numerous products, including bottles, plastic packaging, 3D printing, and plastic bags, employ PE. UV and chemical resistance are both features of PE. Thermoformed plastic goods like shampoo bottles, food trays, containers, and recycling bins may be produced effectively using this method.
- POLYPROPYLENE (PP): The polypropylene segment held the market share of 20.05% in 2021 and is expected to register the CAGR of 5.53% during the forecast period. Manufacturers frequently employ crystalline thermoplastic polypropylene (PP) in common items and applications like household goods, packaging trays, and medical equipment. Due to its unique properties-including, including chemical resistance, flexibility, low electrical conductivity, safety for use around food, minimal water absorption, and-most importantly-its ability to keep costs low for products-PP is frequently employed in commercial production. Products for huge industries like machinery, textiles, and even fibers require propylene.
- POLYSTYRENE (PS): The polystyrene segment held the market share of 7.44% in 2021 and is expected to register the CAGR of 4.62% during the forecast period. Polystyrene (PS) plastic is a naturally transparent thermoplastic found in solid foam and standard solid plastics. PS plastic is frequently utilized in numerous consumer product applications and is very beneficial for business packaging. Polystyrene is a solid plastic frequently used in medical devices like test tubes and Petri dishes. The utilization of polystyrene as the foam is its most distinctive use. Although it dominates the packaging sector, traditional plastics can also be used for various applications.
- ACRYLONITRILE BUTADIENE STYRENE (ABS): The acrylonitrile butadiene styrene segment held the market share of 4.63% in 2021 and is expected to register the CAGR of 3.43% during the forecast period. Acrylonitrile, butadiene, and styrene are the main components of the thermoformed plastic known as ABS. It can withstand temperatures as high as 176 °F and as low as -4 °F. This guarantees that the plastic may be heated to a high temperature and molded into any desired shape. Impact-proof and corrosion-resistant ABS is available. It is, therefore, the perfect material for 3D printing, car parts, safety gear, and home appliances.
- POLYVINYL CHLORIDE (PVC): The polyvinyl chloride segment held the market share of 8.07% in 2021 and is expected to register the CAGR of 4.67% during the forecast period. The most often used material for thermoforming is PVC (Polyvinyl chloride). It is made by suspension polymerization, and because of its robust structure and ability to tolerate impacts and extremely high temperatures, it is the perfect plastic. Additionally, it is an economical plastic, which makes it the material of choice for the majority of sectors. Products, including pipes, flooring, electric wires, and faux leather clothes, are frequently made from PVC via thermoforming.
- HIGH IMPACT POLYSTYRENE (HIPS): The high impact polystyrene segment held the market share of 2.37% in 2021 and is expected to register the CAGR of 4.03% during the forecast period. Various consumer goods are made from the versatile plastic known as HIPS (high impact polystyrene). It is the perfect material for protective food packaging because of its clarity. It has both high tensile strength and good impact resistance. HIPS is a suitable plastic for thermoforming due to its malleability. It retains its characteristics even after being repeatedly bent into various shapes.
- BIODEGRADABLE POLYMER: The biodegradable polymer segment held the market share of 3.51% in 2021 and is expected to register the CAGR of 2.61% during the forecast period. Biodegradable materials are used in packaging, agriculture, medicine, and other industries. Biodegradable polymers have drawn more attention in recent years. Synthetic and natural polymers can be categorized into two categories of biodegradable polymers. There are certain polymers made from feedstocks originating from natural or petroleum resources.
- Others: The others segment held the market share of 1.44% in 2021 and is expected to register the CAGR of 3.27% during the forecast period. The others segment include acrylic, polycarbonate, post-consumer resin, etc. A category of thermoplastic polymers known as polycarbonates (PC) has carbonate groups as part of its chemical makeup. Strong, resilient polycarbonates are employed in engineering, and certain varieties are optically clear. A long-lasting substance is polycarbonate. Large plastic deformations without breaking or shattering are possible with polycarbonate. Acrylic sheet is simple to manufacture, adheres well to solvents and adhesives, and is simple to thermoform. Compared to many other transparent plastics, it offers better weathering characteristics.
By Process
- Vacuum Forming: The vacuum process is renowned for producing goods quickly and affordably. Within the more general definition of the plastic thermoforming process, vacuum thermoforming is a method of making plastic thermoforms. A 2D thermoplastic sheet is heated to the ideal temperature for forming in vacuum forming, and it is then placed over a unique mold or tool. The material is then drawn onto the mold surface to produce the required 3-dimensional part shape after the air between the heated sheet and mold is evacuated, generating a vacuum. It is removed and subsequently treated to specification when the newly molded part has cooled and hardened. It is used when producing items when precision and accuracy aren’t crucial, such as domestic items and packaging.
- Pressure Forming: When more intricate details from the thermoforming process are needed, pressure forming is used. Pressure forming is a production method within the more general definition of the plastic thermoforming process. In pressure molding, a two-dimensional thermoplastic sheet material is heated to an ideal temperature for molding before being placed over a specific mold or tool. The material is subsequently forced into a mold's surface by applying positive pressure over the heated sheet, creating the required three-dimensional part shape. It is used when producing items when durability and uniformity are requirements.
- Mechanical Forming: The mechanical forming segment held the market share of 28.43% in 2021 and is expected to register the CAGR of 3.92% during the forecast period. The preheated plastic sheet is shaped by applying a direct mechanical force in this procedure. The surface patterns are imprinted into the plastic sheet by a core plug, forcing it to fill the space between the plug and the mold. When accuracy and attention to detail are essential, mechanical thermoforming is performed. It is used for manufacturing high-quality and precision items.
By Application
- Packaging: Fresh meat, eggs, fruits, and vegetables are prepackaged in polystyrene thermoformed plastic trays and containers. Shipping, interim packaging, and inventory expenditures are all eliminated as a result. The need for thermoplastics is quite high in the food industry because they provide the higher quality packaging materials that food packaging needs to ensure protection against moisture, odor, and germs. In horticulture, every plant is grown in thermoformed trays. These reusable trays cover the growing seasons. These trays are reasonably priced and mostly made of recyclable materials. The production of flowerpots is the other application, which has transitioned from injection molding to thermoforming. Thermoform plastics are utilized in this industry instead of materials like wood and glass because they are lighter, more flexible, less prone to bacteria, odor- and moisture-free, and limit bacterium growth.
- Construction: The construction industry benefits from vacuum-formed plastic components because they are durable, waterproof, and rigid. Self-colored polymers with matt, gloss, smooth, or embossed finishes that are extremely resistant to UV light and color fading can be used in thermoforming. This makes it simple to apply a variety of colors and keeps the finished product looking polished and lovely for longer. Many of the same features are available in plastic windows made of polycarbonate. These windows are sturdy yet only somewhat heavy. Additionally, they provide security protections, customization possibilities, and clear visibility.
- Automotive: The automotive segment held the market share of 7.68% in 2021 and is expected to register the CAGR of 5.16% during the forecast period. Interior finishing uses thermoformed plastic most frequently. Thermoforming is used to create the backs and armrests of airplane seats, bus and train seats, and fold-down tray tables. Thermoformed plastics are perfect for various automotive components, including doors, dashboards, bumpers, air ducts, truck bed liners, floor mats, and headlamp covers. When necessary, pressure forming produces accurate, sharp features and beautiful surfaces, whereas vacuum forming is best for the bigger, shorter-run components (such as bumpers and interior panels). Thermoformed plastics are good for transporting because of their lightweight construction.
- Electrical & Electronics: The electrical & electronics segment held the market share of 10.27% in 2021 and is expected to register the CAGR of 4.79% during the forecast period. One of the strongest thermoplastic plastics, polycarbonate has exceptionally high impact resistance and, in some circumstances, is even bulletproof. ABS is also quite durable. These two polymers are usually utilized in electronics casings to safeguard all the delicate components that enable our equipment to function. The safest plastics for insulators include ABS and polycarbonate. Nothing will catch fire if an electrical malfunction takes place inside a device. And if something does, the flame will disappear shortly. Due to its lower production costs compared to conventional electronic materials, electronic plastic is becoming more and more popular. Electronics can be more affordable for manufacturers by using plastics more frequently. Due to its lower production costs than conventional electronic materials, electronic thermoformed plastic is becoming popular. Plastics can be used more frequently by manufacturers at a lower cost, allowing for more economical devices without compromising quality.
- Consumer Goods: The consumer goods segment held the market share of 4.83% in 2021 and is expected to register the CAGR of 4.00% during the forecast period. India is a growing market for consumer goods, and packaging plays a big role in the retailing of products through innovative packaging. To achieve new sustainability standards, including reduced material consumption, effective truck space use, effective transportation efficiency, and the use of eco-friendly materials, manufacturers must produce plastic packaging designs that are distinctive and attractive.
- Others: The others segment held the market share of 14.26% in 2021 and is expected to register the CAGR of 2.95% during the forecast period. Thermoformed plastic can also be used in mechanical engineering, appliances, furniture, medical, etc. The door liners of all refrigerators and freezers are thermoformed. Thermoforming is used to create computers, television cabinets, window air conditioners, humidifiers, dishwashers, and clothes dryers. Hospitals, clinics, and physician's offices can order medical supplies such as tools, syringes, needles, tubing, and vials. Medical items, gadgets, and components are safeguarded by thermoformed packaging, which also preserves their sterility and efficacy. Medical products are delivered from the point of manufacture, through distribution, and into the hands of the end user safely owing to their stiffness, durability, and security. Sterile instruments and implants are frequently protected with thermoform packaging. This packing technique allows for thin, transparent plastic enclosures that prevent dust and microbes from contaminating the sterile item.
By Region
- North America: The thermoformed plastics market in North America was the largest geographic segment in 2021. The market is expected to rise rapidly during the anticipated time frame due to industrialization and the expansion of the packaging industry. It is anticipated that this region will see an increase in thermoformed plastic product suppliers and manufacturers. The largest market for thermoformed packaging is the US, followed by Canada.
- Europe: The second-largest market for thermoformed plastics is anticipated to be Europe. The intense consumer and manufacturing environment in Eastern Europe is likely to be the main driver of the demand for thermoformed plastics. Furthermore, regulatory bodies like the European Chemicals Agency (ECHA), the European Commission, and other federal agencies have established several stringent environmental standards defining the European market
- Asia Pacific: The Asia-Pacific segment held the market share of 17.0% in 2021 and is expected to register the CAGR of 6.88% during the forecast period. Asia-Pacific is the region with the fastest anticipated growth. India and China are two emerging economies now experiencing rapid economic expansion. Demand for construction materials, automobile parts, and medical device packaging has been boosted by rising population and disposable income. China is the region's major manufacturer and supplier of equipment using various types of technologies that use thermoformed polymers. Strong economic growth in China helps to support the country's rapid urbanization. This region's rising per capita disposable income is anticipated throughout the forecast period to drive the market.
- Latin America: The Latin American market is divided into Brazil, Peru, and Argentina are the major contributors in the region. held the market share of 9.2% in 2021 and is expected to register the CAGR of 5.10% during the forecast period. The region held the market share of 6.7% in 2021. The growth in the region is attributed to the growth in the construction industry.
- Middle East & Africa: Middle East & Africa UAE is the leading country in the region followed by Turkey and Egypt. Polymethyl methacrylate (PMMA) has seen an increase in inventions, product developments, and investments.
Read More About This Report: thermoformed plastic market share
Leading companies partner with us for data-driven Insights
Kindly complete the form below to receive a free sample of this Report
Companies Covered | 15 |
Pages | 111 |
Certified Global Research Member
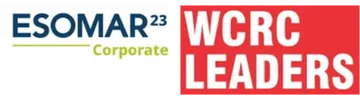
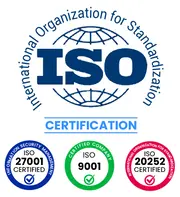
Why Choose Market Research Future?
- Vigorous research methodologies for specific market.
- Knowledge partners across the globe
- Large network of partner consultants.
- Ever-increasing/ Escalating data base with quarterly monitoring of various markets
- Trusted by fortune 500 companies/startups/ universities/organizations
- Large database of 5000+ markets reports.
- Effective and prompt pre- and post-sales support.
Tailored for You
- Dedicated Research on any specifics segment or region.
- Focused Research on specific players in the market.
- Custom Report based only on your requirements.
- Flexibility to add or subtract any chapter in the study.
- Historic data from 2014 and forecasts outlook till 2040.
- Flexibility of providing data/insights in formats (PDF, PPT, Excel).
- Provide cross segmentation in applicable scenario/markets.