Pune, India, Sep 2022, MRFR Press Release/Market Research Future has published a Cooked Research Report on the Global Surface Technology Market.
Surface Technology Market Synopsis
The global surface technology market is projected to witness significant growth during the review period, exhibiting a CAGR of 4.98%. The market is expected to reach a value of USD 4,93,297.7 million by the end of the forecast period. In terms of value, the market size was USD 3,27,349.0 Million in 2021.
Surface technology processes majorly used to extend the working life of materials and components and enhanced the property of material. The process can be used to apply coatings to a wide range of materials and components and imparts resistance against wear, erosion, cavitation, corrosion, abrasion, or heat. The Surface technology process can be classified into six types, namely, high velocity oxygen fuel (HVOF) coatings, plasma, ceramics coatings, anodizing, vapor phase aluminate, slurry coatings, and others. In the energy & power industry, surface technology find uses in energy conservation, i.e., for the fabrication of solar panels in the form of transparent conductive coatings. In contrast, ceramic coatings are used in fuel cells and batteries. Additionally, ceramic coatings are used in the hot gas area of stationary gas turbines, as cation-conducting ceramics in low-loss high-power batteries or as corrosion-resistant dielectrics in molten carbonate fuel cells.
Competitive Landscape
Amid intensifying competition, key market players are focusing on research and development activities for introducing innovative technologies with efficient and cost-effective features. Besides this, they are establishing their bases in attractive regions of Asia, Africa and the Middle East.
Key players in the market are Bodycote, DOWA Thermotech Co., Ltd., Schaeffler Group, Linde Plc, Aalberts Surface technology, Guangdong Strong Metal Technology Co., Ltd, Harterei Reese, FPM Heat Treating, Paulo, Surface Technology, Inc. According to the present scope of the study, Bodycote is the top participant in the surface technology market sector, owing to its comprehensive product offering and widespread availability of commodities. DOWA Thermotech Co. Ltd.is the second-largest player, followed by Schaeffler Group, Linde Plc, and Aalberts Surface technology.
Segmentation
By Type
- High Velocity Oxygen Fuel (HVOF) Coatings: High Velocity Oxygen Fuel (HVOF) coating is a thermal spray process in which a fuel and oxygen are mixed, fed into a combustion chamber, and ignited. The gas produced in the combustion chamber has a very high temperature and pressure, and it is ejected at supersonic speeds through a nozzle. Powder is injected into a high-velocity gas stream and propelled toward the coating substrate. As a result, the coating has a low porosity and a high bond strength to the substrate material, making it wear and corrosion resistant.
- Plasma: Plasma surface treatment is a method of increasing the surface energy of a variety of materials in order to improve bonding properties. Corona treatment is a term used to describe one type of plasma treatment. Plasma technology is used for a variety of surface treatment applications, including cleaning, coating, printing, painting, and adhesive bonding.
- Ceramic Coatings: Ceramic Coatings are a silica or quartz-silane-based synthetic chemical product. They're referred to as permanent coatings because they can't be removed unless you use compounding/polishing or deliberately ignore them. Coatings for various applications are prepared using ceramic coating technology.
- Anodizing: Anodizing is a process for coating aluminum with protective and decorative oxide layers that improve corrosion resistance and wear resistance. Dyeing or electrolytic coloring are used to create various colors. Anodizing is long-lasting, environmentally friendly, and precise in terms of tolerance.
- Vapor Phase Aluminate: Vapor Phase Aluminate (VPA) coating is an above-the-pack process that involves placing components in a heated inert atmosphere surrounded by CrAl donor material. The donor material does not come into direct contact with the parts. In the presence of a carrier gas, the aluminum in the donor material and the halide activator vaporizes and condense onto the target parts during thermal processing.
- Slurry Coatings: Slurry coating involves dipping or spraying a slurry mixture containing the coating elements onto a substrate surface, followed by a thermal treatment in a protective environment. Vapor transport, liquid reaction, or solid-state sintering are all methods for coating formation. For the formation of high-temperature coatings on composites, slurry processes have been widely used.
- Others: Others segment include combustion spraying, liquid coating, electric arc wire, flame spraying, etc.
By Application
- Aerospace: Aerospace segment is further bifurcated into engine, structural, hardware, and others. Oxidation resistance, corrosion resistance, wear resistance, heat resistance, fatigue resistance, and special functions of products and components are becoming increasingly important in the rapidly growing aerospace industry.Thermal barrier coatings (TBCs), environmental barrier coatings (EBC), high-temperature abradable sealing coatings, wear-resistant coatings such as WC-Co and aluminum oxide titanium, absorbing and infrared stealth coatings, and others are among the rapidly developing aviation surface treatment technologies.
- General Industrial: General Industrial segment is further bifurcated into wind turbine, land bases, and marine & defense. Wind turbines benefit from surface technology that provide long-term protection against erosion, corrosion, and wear and tear. Aluminizing, platinum coating, electron beam physical vapor deposition, plasma spraying, and low vacuum plasma spray (LVPS) are examples of Surface technology. Land bases include satellite bases, ground-based air systems, and remote stations, etc. Barnacles, mussels, and microorganisms that cling to ships are a constant and costly nuisance for commercial and recreational ships.
- Automotive: Engine and power train components, for example, rely not only on their bulk material properties, but also on their design and surface characteristics. Their surface must perform engineering functions in a variety of complex environments in these components. These automotive components' surfaces may need to be treated to improve their surface characteristics. Surface coatings in automotive components can improve corrosion resistance, surface hardness, and weight reduction in addition to providing wear protection.
- Power Generation: Power generation equipment makes use of sophisticated, advanced-technology machines that require a significant amount of time, money, and effort to optimize. Advanced surface coatings, weld overlays, and ancillary processes are thus cost-effective and practical options for preventing and controlling corrosion, wear, fouling, and high-temperature oxidation of components in your power generation equipment. Surface technology extend component lifespans, reduce replacement costs, and reduce the number of service outages. It also reduces downtime, reduces the risk of damage, and improves turbine efficiency.
- Building & Construction: The building and construction business demands windows, façades, and roofs to have a long usable life and to provide constructional and decorative design options. Surface coatings includes antimicrobial coatings, food coatings, energy-saving coatings, smart glazing, hydrophilic, hydrophobic, and super hydrophobic coatings, corrosion protection coatings, barrier coatings, and paints.
- Oil & Gas Pipeline: The two basic types of degradation that impact steel and light metal alloys utilized in upstream production applications are environmentally assisted cracking and localized corrosion. Particularly those classified as HPHT, Arctic, or sour. Sour fields are distinguished by detectable levels of hydrogen sulfide.
- Food & Beverages: A variety of coatings are used in the food and beverage industry to improve the performance of processing and packaging machinery by enhancing surface release and reducing friction. Many production lines benefit from friction without sticking. Fresh dough, for example, is a stubborn substance whose surface coating prevents adhesive particles from sticking to conical molders and allows production to run quickly.
- Textile: The abrasive properties of man-made fiber, particularly nylon, polyester, glass, and carbon, along with the corrosive properties of additives like fiber lubricants, erode yarn contact surfaces. This might result in expensive downtime while machine parts are replaced, or, worse, damage yarn quality. Ceramic and tungsten carbide coatings are utilized on many parts in the fiber producing, textile processing, and non-woven sectors to help fiber producers and processors handle these challenges, such as feed rollers, guides, bars, pins, thread wheels, and rotary, storage, and friction discs.
- Paper & Packaging: From paper machine rolls to doctor blades on dryer drums to press and anilox rolls, protect most critical components from abrasive wear and corrosion while improving the quality of each sheet of paper, board, tissue and towel. Machine calendar, soft calendar, and supercalender rolls with chromium and tungsten carbide coatings maintain surface finish, smoothness, and gloss while extending roll life. Ceramic coatings on center press, wire, and dryer felt rolls reduce corrosion, wear, and static buildup.
- Metallurgy & Minerals: To maintain a competitive edge, there is growing demand for the highest-quality aluminum or steel in the most cost-effective way possible. Wear- and corrosion-resistant coatings applied by thermal spray and laser weld overlay maintain quality, reduce costs, extend the service life of critical rolls, and prevent unplanned outages due to roll surface failures.
- Others: Others segment include glass coating, chemical processing equipment, pharmaceutical processing equipment, reciprocating compressor plungers & piston rods, and plastic industry.
By Region
- North America
- Europe
- Asia-Pacific: Asia-Pacific market is poised to register the highest growth rate in the forecast period owing to the favorable funding for academic research, rising focus of key market players in this region, developing R&D infrastructure, increasing research collaborations with the U.S. and European countries, and increasing R&D expenditures by pharmaceutical companies. Growth in the Asia-Pacific region will be driven by developing countries such as India, China, Singapore, South Korea, and Japan.
- Latin America
- Middle East & Africa
By Region
- North America: In North America, market is primarily driven by the growth of the automotive, aerospace, and key manufacturing industries also availability of low-cost raw materials and labor, coupled with the increased spending power, is a major driver for the market in this region. surface technology is gaining attention from power generation sector.
- Europe: The European automotive industry accounts for more than 90% of total region. Germany has led the European automotive market, and it is expected to continue to do so throughout the projected period.
- Asia-Pacific: Asia-Pacific market is poised to register the highest growth rate in the forecast period owing to the favorable funding for academic research, rising focus of key market players in this region, developing R&D infrastructure, increasing research collaborations with the U.S. and European countries, and increasing R&D expenditures by pharmaceutical companies. Growth in the Asia-Pacific region will be driven by developing countries such as India, China, Singapore, South Korea, and Japan.
- Latin America: The surface technology industry in Latin America is primarily driven by the growth of the automotive, aerospace, and key manufacturing industries. Increased application of engineering plastics in various industries such as aerospace, automobile, defense, and electrical and electronics is boosting the demand for surface technology in Latin America.
- Middle East and Africa: In this Middle East and Africa, usage of surface technology in the automotive sector is one of the driving factor for the market. Fuel efficiency and emission standards have compelled automotive manufacturers to shift their focus toward the inculcation of nylons in various applications such as powertrain, chassis, trim components, and other sectors.
Access full report @ surface technology market size
Leading companies partner with us for data-driven Insights
Kindly complete the form below to receive a free sample of this Report
Companies Covered | 15 |
Pages | 100 |
Certified Global Research Member
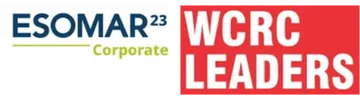
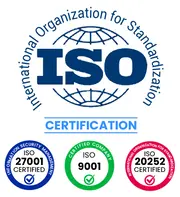
Why Choose Market Research Future?
- Vigorous research methodologies for specific market.
- Knowledge partners across the globe
- Large network of partner consultants.
- Ever-increasing/ Escalating data base with quarterly monitoring of various markets
- Trusted by fortune 500 companies/startups/ universities/organizations
- Large database of 5000+ markets reports.
- Effective and prompt pre- and post-sales support.
Tailored for You
- Dedicated Research on any specifics segment or region.
- Focused Research on specific players in the market.
- Custom Report based only on your requirements.
- Flexibility to add or subtract any chapter in the study.
- Historic data from 2014 and forecasts outlook till 2040.
- Flexibility of providing data/insights in formats (PDF, PPT, Excel).
- Provide cross segmentation in applicable scenario/markets.